Price Engineering Takes Hydraulic Technology for a Spin
By Arthur Thomas – Milwaukee Biz Times
August 8, 2016
The concept behind Hartland-based Price Engineering’s latest development is fairly straightforward. Air bubbles can be removed from hydraulic fluid faster by spinning the oil instead of letting it sit and waiting for gravity to do the work.
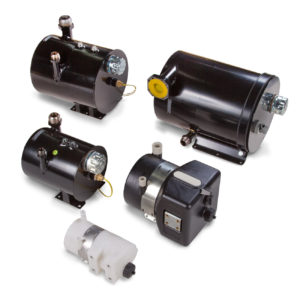
The air, which enters the oil through lower pressure areas in a hydraulic system, needs to be removed to keep the system operating as intended.
Traditionally, the air is removed by leaving the oil to sit in a reservoir tank. The size of the tank is generally dictated by the size of the pump and can be as large as five times the displacement of the pump. A 10-gallon pump could require a 50-gallon tank to keep enough oil available for the system.
A large tank doesn’t necessarily fit inside an engine compartment or in other mobile applications, so the industry has gone toward a one-to-one ratio as the standard.
The cyclone hydraulic reservoir developed by Price Engineering seeks to reduce the size and weight of the tank by 90 percent by reducing the amount of oil needed.
To make those reductions possible, Price’s design uses centrifugal force to spin the air bubbles out of the oil. As the fluid returns from the system, it is forced into the cyclone reservoir. The heavier fluid molecules stick to the walls as the air bubbles begin to rise to the top. A flow-directing piece called a baffle separates the upper and lower chambers while facilitating the cyclone action. The oil can be in and out of the reservoir within three seconds.
The concept itself isn’t unique to Price and the original design for using the technique in hydraulics is actually patented by Eaton Corp. Price pays a royalty under a licensing agreement with Eaton, but has also taken the product much farther.
It hasn’t been a straight path to get to the point Price reached this summer, introducing a complete line of cyclone tanks in different sizes and materials.
The product Eaton created was made of plastic and came in one size, said Terry Glidden, managing director for hydraulics at Price. Eaton wasn’t interested in developing the product further, but did work out the licensing deal with Price.
Price’s development of the technology started with steel, but it found limited success. The amount of welding required – for the baffle, mounts and other components – drove the price up.
The original design from Eaton was made of plastic, but it was molded in three pieces and glued together. The original equipment manufacturer Price was working with had seen similar designs literally shake apart, Glidden said. In some cases, OEMs require the tanks to withstand being shaken at 150 cycles per second.
“The big discovery was understanding how to make this in a one-piece, integral, rotational mold,” he said, adding that blow or injection molding would be difficult, if not impossible, to use in Price’s application.
After finding a technique to address the cost of welding and the durability of using multiple pieces, Price had nearly completed its development. The one remaining challenge was to make it possible to check the oil level without the need for a gauge.
“Our objective all along was to mold it in a way you could see through,” he said.
Enter Solar Plastics Inc., a Minnesota-based company that does the rotational molding for Price. The company brought Price a nylon material made from rapeseed oil. While other materials came out with a yellowish hue, this particular grade of nylon was clear enough to negate the need for an additional device, saving more room.
Because of all the changes Price made, the machines will need less hydraulic oil, the reservoir takes up less space and the overall weight is reduced.
“Less weight means you can carry more of the stuff the machine is meant to carry,” Glidden said.
Price estimates that replacing a 20-gallon reservoir with the equivalent cyclone tank can save $270 on fluid costs, $300 in annual fuel costs from reduced weight and three cubic feet of space on the vehicle.
While the lower portion of the reservoir is key to the cyclone design, the upper part can be made into any shape a customer needs, Glidden said. This allows a tank to fit into tight spaces.
The cyclone technology isn’t a perfect fit for all applications, but Glidden said it can work particularly well in environmentally sensitive situations. He cited turf care, pleasure craft, work boats and weed harvesters as examples. Carrying less oil means less environmental impact if a spill does occur.